buy ExtendSim Pro | trial version
Use ExtendSim Pro’s Discrete Rate module to simulate high-volume or bulk-flow processes, high-speed systems such as packaging lines, chemical processes, network traffic, and any other rate-based process that can be described in terms of tanks, levels, and valves. In these systems the rates are recalculated when events occur, affecting how fast the product moves and what the yields will be given the model’s constraints and configuration.
Discrete rate simulation (DRS) combines the event scheduling features of discrete event simulation with the rate-based capabilities of continuous simulation to uniquely address a range of systems that cannot be adequately modeled using the discrete event or continuous simulation methods. DRS is used to model linear continuous systems, hybrid systems, and any other high speed/large volume system that involves the rate-based movement or flow of material between locations, calculating new flow rates when events occur. The materials could be liquids, solids, powders, gases, particles, data, or any other type of fungible or bulk element.
Use the Rate module in ExtendSim Pro to:
- Simulate rate-based flows of “stuff”: homogeneous products; high volume, high speed, or bulk production; data feeds and streams; liquids and gases; and any rate-based movement of otherwise distinct entities where uniquely identifying the entities is either unneeded or unwanted.
- Model oil and gas production, refining operations, minerals and mining, power systems and grids, petrochemical and chemical processing, high speed packaging and production lines (food and beverage, pharmaceuticals, paper), water treatment plants, and more.
- Maintain and adjust manufacturing recipes. Size production batches, tanks, silos, hoppers, etc. Experiment with different equipment configurations.
- Control flow, manage rules, and test constraints while reducing waste of unwanted product.
- Combine with discrete event and reliability modeling to represent entire systems and supply chains.
The ExtendSim Rate module includes:
- Components for simulating the flow of bulk materials such as powders, fluids, minerals, and chemicals or the production, mixture, filling, and packaging of large quantities of things such as cereal, soap, cans, and bottles.
- Customizable flow attributes to provide information about the flow and organize quantities or volumes of flow into layers.
- Set indicators (set points) to report when a tank’s flow level is within a specified range. Convey Flow block has multiple modes (accumulating, non-accumulating) and sensors for communicating the density of flow over time at points along the conveyor.
- Constraints and paths for realistically routing the flow.
- Merge and diverge flow using rule-based options such as distributional, priority, and proportional
Why simulate using Discrete Rate simulation?
The ExtendSim Discrete Rate module has been specifically designed to simulate the behavior of bulk flows and high speed processes so that engineers and analysts in mining, energy, consumer products, process industries, and many other fields can solve problems and quickly get answers.
A natural fit
A discrete rate approach to modeling is well-suited for simulating high-volume bulk flows, high-speed processes, and aggregated materials or substances because they have a lot in common. They:
- Often require specialized equipment.
- Have high operating costs.
- Are subject to maintenance issues and shutdown.
- Have complex system interactions which are further compounded by the presence of discrete and continuous flows of material at different steps in a process.
Advantages
The advantage of discrete rate simulation is that it allows you to:
- Perfect processes and products.
- Plan resource capacity by determining the rate at which products are being processed or sold.
- Test various schedules to maximize process efficiency.
- Identify bottlenecks and determine throughput.
- Evaluate system reliability.
- Fine-tune distribution control strategies.
- Study system constraints and the impact of rate changes.
- Evaluate plant configurations.
- Analyze the effect of processes on the internal and external environment.
Technology Behind the Rate Constructs
ExtendSim's Rate module utilizes linear programming (LP) to calculate the flow within these types of systems then solves the LP to maximize rates when algebraic methods are insufficient. This global approach has been proven to be a reliable, computationally efficient, and broadly adaptable DRS technology.
How it works is that during a simulation run, flow moves at a certain speed, called the effective rate; between events, the rate of flow stays constant. The movement of material between locations that hold or route the flow follows paths, rules, and constraints that are set in the model. Calculation occurs only at discrete events - such as equipment failure, a product change-over, or a tank reaching full capacity - that would cause a change to one or more effective rates. There is no concept of delta time (Δt) in discrete rate simulation. Instead, the simulation clock updates only when events occur. The discrete event calendar used by the discrete rate simulation maintains a list of future planned events. It is interesting to note that a single event may be rescheduled many times, adapting its predicted time of occurrence because of other system events. For example, if the flow rate into a tank changes, the predicted time that a tank will be full or empty is adjusted. |
Learn more... Discrete Rate Simulation Using Linear Programming by Cecile Damiron & Anthony Nastasi • Imagine That Inc. A Global Approach for Discrete Rate Simulation by Cecile Damiron & Dave Krahl • Imagine That Inc. |
Discrete Rate vs Discrete Event and Continuous Simulation
Discrete rate simulation is similar to continuous simulation in that they both simulate flow and recalculate flow rates, which are continuous variables. DRS differs from continuous simulation in that it is event-based; it does not simulate every time step. DRS is also similar to discrete event simulation in that both utilize event-based timing. However, while discrete event simulation assumes there is no change in the system between consecutive events, in a DRS model flow continues to move between events, although at a constant rate. Furthermore, DRS models are concerned with the status (quantity and location) of homogeneous flow, rather than the status of discrete system entities.
- If a linear continuous system is modeled with continuous simulation, a time step must be chosen that is sufficiently small to minimize error. Since state change events can occur between time steps, precision errors will happen no matter how small the time step is. Plus smaller time steps negatively affect model performance.
- If the system is modeled as discrete event, the modeler must choose a “chunk size” or amount of material that a single item represents, dividing the flow into discrete entities. When flow is artificially discretized, the simulation has the same precision issues as with continuous. Here, as well, the modeler will have to trade off accuracy for performance.
Neither continuous nor discrete event simulation are as accurate for linear continuous systems as discrete rate, and the approximations and assumption caused by those two approaches often result in models that can be poor predictors of real-world systems. | Related article... Comparison of Discrete Rate Modeling and Discrete Event Simulation. Methodological and Performance Aspects by Jacek Zabawa and Edward Radosinski • Wroclaw University |
Combining Discrete Rate Simulation with Reliability Block Diagramming
Yogurt Production:
Combining discrete rate technology with reliabilityOn their own discrete event, discrete rate, and reliability block diagramming (RBD) are powerful analysis tools. Imagine the power of combining these technologies in one tool. It's like baking a cake...the cake on its own tastes amazing, but add icing and a filling and its simply spectacular! That's the synergy of combining the ExtendSim Reliability module with ExtendSim's DE and DR technologies...simply spectacular!
There are a number of compelling advantages to combining these technologies:
- More accurate wearing. The process model can be used to define when certain types of machine wearing is occurring on the resources in the RBD. This can lead to a more accurate assessment of when wear-based failures occur.
- Detailed repair modeling. When a resource in the RBD fails, ExtendSim modeling capabilities can be used to break out the repair process in as much detail as needed:
- Are the tools needed to make the repair currently available?
- What is the current level of spare parts inventory?
- Are the labor resources qualified to make the repair currently available or are they performing other work?
- Should we preempt key resources and redirect them to this higher priority job?
- If the resources required to make this repair are currently unavailable, should we outsource the job?
- The RBDs ability to model when resources and/or entire systems are down can be used to impact the movement of material through the simulated process. This allows the modeler to explore the relationship between resource availability and system performance metrics like throughput, production costs, repair costs, utilization, inventory, service levels, etc.
Examples Using Discrete Rate Simulation
The ExtendSim Discrete Rate Simulation technology was developed more than 15 years ago. It was a revolutionary advancement at that time and continues to be the leading discrete rate simulation technology available today. Building upon numerous customer experiences and taking advantage of newer methodologies, the ExtendSim DRS technology is now in its third generation. As you might expect, it has been used extensively in industry, especially for:
Mine to market coal supply chain - testing stockpile management strategies in a planned materials handling facility (MHF) plus testing competing capital investment options for moving coal from the MHF to a planned rail head.
- Processing plant - optimization of a plant’s internal water recycling system to minimize use of costly outside water.
- Food processing plant - manage aging of products in intermediate stocks, maintain strict constraints of hygiene/sanitation, and study new equipment layout in preparation for product increases.
- Chemical companies - major chemical companies use ExtendSim DRS to simulate chemical plant operations and identify the processes that limit plant production. DRS captures plant dynamics and successfully identifies different bottlenecks for each product. The models are also used to evaluate the costs and benefits of proposed solutions and to improve the production capability of the plants.
- Mining companies - use ExtendSim DRS to develop pit-to-port and mine-to-market models of coal supply chains. A model at one international mining company tests stockpile management strategies in a materials handling facility (MHF) and analyzes competing capital investment options for moving coal from the MHF to a rail head.
- Consumer products companies - use ExtendSim DRS to model and analyze their high speed production lines and to test production scheduling as well as different production speeds for bulk material. One multinational company simulates the high speed production and packaging of laundry detergent. This allows them to test production schedules when adding new products and helps them manage intermediate stock between production and packaging. Another company performs reliability studies and tests production policies (start and stop times, batch levels, rework, etc.) based on the type of bulk material.
- Commodities producers - use ExtendSim DRS to simulate production, harboring, and shipping routes for liquid natural gas. Models help determine the number and size of ships required as well as the amount of on-land storage needed. The impact of the external environment, including wind levels, visibility, and so forth, are included as part of the simulation.
- Major American food company - uses DRS to simulate the production of peanut butter. The model explores various configurations for the company’s conveyor belt system, including expected and unexpected shutdowns, and conveyor length, speed, and capacity. The goal is to reduce bottlenecks and maximize throughput. Different systems supplying and demanding material at various rates, quantities, and operational shifts introduces complexities the model readily solves..
- Water and Wastewater management
- Pharmaceutical, Oil, Polymer, Paint
Case Studies


High Accuracy Discrete Rate and Reliability Modeling to Drive Improvement of Plant OEE and Throughput
Lawrence Fischel, Clorox Services Company & Tom Lange, Technology, Optimization, and Management
Presented at the 2020 Winter Simulation Conference
December 2020
For Hidden Valley Ranch salad dressing, increased demand required increased production capacity. Rather than obtain additional equipment, improved efficiency was sought using modeling and simulation. Using existing, historical plant data for line event status in JMP Statistical software, failure-mode-specific uptime and downtime distributions were obtained. Using these distributions in an ExtendSim discrete rate and reliability model, the simulation matched the actual data within 1% Overall Equipment Effectiveness (OEE). This high accuracy model enabled prioritization of equipment and procedural improvements and exploration of product selection, run rate, and buffer size changes. Several counterintuitive improvements were identified. Even though increasing the production rate also increases the failure rate, the overall throughput increases. Frequent, short duration stoppages might seem innocuous; however, the integrated cooperativity of the production line magnifies the effects. Visually understanding the impact of their actions on the line stimulated increased vigilance as well as increased agency in the operations staff.
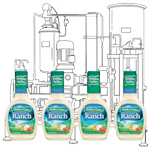