buy ExtendSim Pro | trial version
The availability of critical resources to perform work is often a key factor in limiting system performance. Yet identifying which resource availabilities are most important, and to what extent the timing and duration of their unavailability impacts the system, can be a complex problem to solve. This is where the ExtendSim Reliability module included in ExtendSim Pro comes into play.
The Reliability module for ExtendSim Pro is a graphical interface for building reliability block diagrams (RBDs) and determining resource availability. It can be used as either a standalone RBD tool or in conjunction with ExtendSim simulation capabilities.
- Analyze the impact of resource availability on system performance.
- Capture reliability behavior and assist in defining repair policies.
- Illustrate how each component’s availability status impacts the status of surrounding components and the status of the system as a whole.
- Store time-between-failure (TBF) and time-to-repair (TTR) random distribution definitions, associating any number of failures, shifts, and maintenance events with a particular component for accurate availability modeling.
- Graphically and statistically describe when scheduled downs (maintenance and off-shifting) and unscheduled downs (failures) occur for individual resources and what impact that has on the availability of the entire system.
- Use as a standalone RBD tool to determine how resource and component availability affect system performance. Capture complex availability behavior of both individual resources and entire systems.
- Explore the relationship between component reliability and component redundancy, spare parts inventory, resource management, and maintenance.
- Simulate systems by combining it with the Item and/or Rate libraries. Since the Reliability module seamlessly integrates with those libraries, you can explore the impact of resource availability on key process metrics such as throughput, production costs, repair costs, utilization, inventory, service levels, and so forth.
This reliability-block-diagramming (RBD) module is the first and only RBD tool to be fully integrated with a process simulation tool.
Why Choose RBD in ExtendSim over a Dedicated RBD Tool?
On the surface, a typical ExtendSim reliability model looks identical to a dedicated RBD tool's model. But the engine underneath the ExtendSim RBD is far more powerful.
Think of it this way, though they are great tools that can accomplish certain tasks, most dedicated RBD tools lack a level of accuracy. They use a black box method to calculate mean-time-to-repair (MTTR) and mean-time-between-failures (MTBF) so there’s no real knowledge of the inner workings of the process. Simulation adds transparency to the data. Some dedicated RBD tools have recognized the need to add a level of simulation to their tools, but simulation is just not their forte so is typically rudimentary at best.
What puts the ExtendSim Reliability module in a league of its own is that it is a simulation package first which has integrated standard reliability block diagramming capability. Simulation is the cornerstone of the RBD, not just an afterthought.
Process Simulation Software vs Reliability Block Diagramming
Even though both the Process Simulation Software (PSS) and Reliability Block Diagramming technologies employ discrete event techniques to manage the simulation clock, historically, the two technologies evolved independently of each other because they were used to solve different kinds of problems. Consequently, very little cross-pollination of ideas and capabilities has transpired between these two technologies.
As a result, PSS and RBD tools benefit from a different set of strengths and suffer from a different set of weaknesses. PSS tools are really good at capturing detailed system behavior, a weakness to dedicated RBD tools. While RBD tools can deliver the kinds of reliability policy and availability analysis that the PSS tools have never dreamed about. ExtendSim Pro bridges this gap by integrating an advanced RBD tool with the ExtendSim PSS capabilities.
Combining RBD with DE and DR Simulation
Yogurt Production:
Combining discrete rate technology with reliabilityOn their own discrete event, discrete rate, and reliability block diagramming are powerful analysis tools. Imagine the power of combining these technologies in one tool. It's like baking a cake...the cake on its own tastes amazing, but add icing and a filling and its simply spectacular! That's the synergy of combining the ExtendSim Reliability module with ExtendSim's DE and DR technologies...simply spectacular!
There are a number of compelling advantages to combining these technologies:
- More accurate wearing. The process model can be used to define when certain types of machine wearing is occurring on the resources in the RBD. This can lead to a more accurate assessment of when wear-based failures occur.
- Detailed repair modeling. When a resource in the RBD fails, ExtendSim modeling capabilities can be used to break out the repair process in as much detail as needed:
- Are the tools needed to make the repair currently available?
- What is the current level of spare parts inventory?
- Are the labor resources qualified to make the repair currently available or are they performing other work?
- Should we preempt key resources and redirect them to this higher priority job?
- If the resources required to make this repair are currently unavailable, should we outsource the job?
- The RBDs ability to model when resources and/or entire systems are down can be used to impact the movement of material through the simulated process. This allows the modeler to explore the relationship between resource availability and system performance metrics like throughput, production costs, repair costs, utilization, inventory, service levels, etc.
Reliability Module Features
The ExtendSim Reliability module has many features that make it a powerful tool for analyzing the role resource availability plays in system performance and determining how to better manage the resources in terms of redundancy and maintenance scheduling. ExtendSim Pro's Reliability module includes:
- Graphical diagram/database builder. The Reliability module provides a graphical interface for building RBDs. As the user builds the diagram, the databases needed to support that diagram are automatically built.
- RBD/PSS interface. The Reliability module is fully integrated and supports communication between the RBD and PSS sections of the model.
- Distribution scaling. Since Time-Between-Downs (TBD) and Time-Between-Ups (TBU) distributions are stored in a generic format in the RBD databases, importing distributions from an external source (such as Excel) is supported. This means the number of distributions needed to support an RBD scales up easily.
- Multiple event cycles per node. To accurately model resource and system availability, any number of different event cycles such as failures, repairs, shifts, and maintenance events can be associated with a particular RBD node.
- Event cycle scaling. Since event cycles are stored in database tables, importing event cycles that have been defined in an external data source is supported. This makes it easy to scale up the number of Reliability Event Cycles (RECs) used to support a model. By default ExtendSim Pro provides the ability to define up to 100 RECs per model, which is sufficient for most applications. If you need more RECs you can purchase ExtendSim Pro outright with either 1000 or an unlimited number of RECs or you can purchase bundles of additional RECs as your business grows and you need additional event cycles for your models.
- Control logic. Optionally, the ExtendSim Integrated Development Environment (IDE) can be used to write code to control all aspects of a node’s behavior. For example, you can write code to control the speed at which a component progresses towards its next down based on any number of factors including the status of other related components, the state of the process model, seasonal policy changes, projected demand, and so forth.
- RBD databases. These auto-built databases contain all the information needed to characterize the structure and current state of the RBDs in a model and document all the results from model runs. Additionally, these databases can be used to control RBD behavior during the run.
Reliability Event Cycles (RECs)
Event Cycles (also known as failure modes) describe a resource's availability behavior over time. To accurately model resource and system availability in ExtendSim Pro, you statistically define Reliability Event Cycles (RECs) to represent failures, repairs, shifts, and maintenance events.
RECs are stored in an internal RBD database that uses the reliability distributions to control how components (resources) move between their up and down states over time. Since they are stored in database tables, importing event cycles that have been defined in an external data source is also supported. This makes it easy to scale up the number of event cycles used to support a model.
By default, ExtendSim Pro provides the ability to define up to 100 RECs per model, which is sufficient for most applications. If you need more RECs you can purchase ExtendSim Pro outright with either 1000 or an unlimited number of RECs or you can purchase bundles of additional RECs as you need them.
Please see ExtendSim Pricing for cost, part numbers, and links to purchase ExtendSim Pro.1000 RECs, as your business grows and your model requires more event cycles, you can purchase additional REC's for your ExtendSim Pro product:
Case Studies
The first simulation tool combined with Reliability Block Diagramming components was introduced by ExtendSim in late 2018. Though the product is still young, many simulationists have found it indispensable in their projects:

High Accuracy Discrete Rate and Reliability Modeling to Drive Improvement of Plant OEE and Throughput
Lawrence Fischel, Clorox Services Company & Tom Lange, Technology, Optimization, and Management
Presented at the 2020 Winter Simulation Conference
December 2020
For Hidden Valley Ranch salad dressing, increased demand required increased production capacity. Rather than obtain additional equipment, improved efficiency was sought using modeling and simulation. Using existing, historical plant data for line event status in JMP Statistical software, failure-mode-specific uptime and downtime distributions were obtained. Using these distributions in an ExtendSim discrete rate and reliability model, the simulation matched the actual data within 1% Overall Equipment Effectiveness (OEE). This high accuracy model enabled prioritization of equipment and procedural improvements and exploration of product selection, run rate, and buffer size changes. Several counterintuitive improvements were identified. Even though increasing the production rate also increases the failure rate, the overall throughput increases. Frequent, short duration stoppages might seem innocuous; however, the integrated cooperativity of the production line magnifies the effects. Visually understanding the impact of their actions on the line stimulated increased vigilance as well as increased agency in the operations staff.
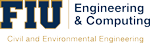
Operational Reliability Assessment of a Remotely-controlled Siphon System for Draining Shallow Storage Ponds
Linlong Bian, Vivek Verma, Aditia Rojiali, Sumit R. Zanje, Dogukan Ozecik, and Arturo S. Leon
Department of Civil and Environmental Engineering, Florida International University
Supported by an ExtendSim Research Grant and the National Science Foundation
2021
Using the ExtendSim Reliability module simplified the maintenance process of a complex system. An optimized architecture of a siphon system was modeled providing accurate results of the system's component reliability, the mean time to failure, and the operational reliability of both non-repairable and repairable systems. Plus, ExtendSim allowed over 10,000 simulation runs to be completed in a short amount of time.
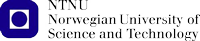
Reliability Modelling of ERTMS/ETCS
Raja Gopal Kalvakunta
Department of Mechanical and Industrial Engineering, Norwegian University of Science and Technology
Supported by an ExtendSim Research Grant and Bane NOR
June 2017
The European Railway Traffic Management System/ European Train Control System (ERTMS/ETCS) is a relatively new system for the interoperability of railways among different European nations. Its complex infrastructure consists of various systems on trackside, lineside, and train onboard and these systems have different sub-systems comprising of software, hardware, network and signalling components. Due to its complexity, determining the failures and resolving them is challenging. A model of the Bane NOR Østfoldbanen Østre Linje (ØØL) ERTMS pilot line was built using the ExtendSim Reliability module incorporating a combination of single station and bidirectional (BiDi) sections. 1000 simulations were conducted to assess ØØL ERTMS infrastructure. It is estimated from the simulation results that this model has the potential to determine the performance of the infrastructure, and it is deduced that predominant infrastructure failures that cause delays are due to partial interlocking fail, maintenance and track fracture, followed by failure of balise, axle counters, and points.
Videos


Using the Reliability Module for Stand-Alone or Integrated RBDs
January 2019 | 1:04:17
Dig into the ExtendSim Reliability module and come out with a sound understanding of its fundamental concepts, including:
- Basic concepts and definitions of reliability
- Creating distributions and event cycles
- Creating reliability block diagrams
- Using RBD in discrete event or discrete rate models
- Setting up wear and shifts in RBDs

Modeling Reliability with ExtendSim
May 2014 Simulation Master Class | 51:19
Discusses the different methods of modeling reliability in ExtendSim. Includes a sneak pre-release peek of the Reliability module as it was under development.