A wave of significant change is moving through the consumer packaged goods (CPG) industry redefining how companies grow, operate, and manage risk. Energy and raw material costs are on the rise, nutritional requirements are constantly changing, increased competition is lowering profit margins - so how do you improve efficiencies in production and distribution to gain an advantage?
The manufacturing process is complex - managing equipment design, plant layout, optimal mix/cook cycle, product packaging, transportation of end product, etc. On top of that, CPG manufacturers are confronted with numerous risk and regulatory issues that government and other regulatory bodies are putting into place. What do you do?
This might be the one time you want to follow the crowd and use ExtendSim.

Food
Processing
For decades, Procter & Gamble has been using ExtendSim to develop and maintain a reliable formula for the relationship between the moisture content of peanuts and the time needed to roast the peanuts before making them into peanut butter. Their ExtendSim model allows them to control roaster settings as well as predict product flow under different moisture conditions.
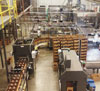
Distribution
Center
A distribution center for a brewery industry leader was fully designed using simulation as a support decision tool. The simulation model took into account all the tasks performed by the distribution center, from the replenishing activities from plants to the very picking of the orders and the load of distribution trucks. Sizing included all the resources: manpower and their work schedules, quantity of forklifts, and space needed.
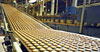
Packaging
Line
A popular cookie producer models their packaging line to understand the dynamics and capacity of their system. Their model shows the effect of changing the speed of a piece of equipment, the failure and repair rates for that piece of equipment, the size of in-line storage, and the mixing of different products.
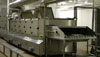
Production
Requirements
A thermo processed meat producer tried to determine the production requirements, in terms of number of ovens and cooling plates it would be required for the production of a certain volume of frozen-cooked meat.The mentioned requirements were dimensioned using simulation to verify the production levels and the utilization ratio of the equipment under different conditions of product-mix, crews, and shift scheduling.
ExtendSim use in the Consumer Packaged Goods Industry
- Food and beverage manufacturing facilities.
- High volume, high speed flow operations.
- Sustainability and traceability.
- Risk assessment and food safety.
- Inventory management.
- Production planning and scheduling.
- Supply and cold chain management.
- Packaging and bottling operations.
- Optimizing perishable and substitutable inventory management systems.
Who is Using ExtendSim
Over-utilized inventory locations at one of its grocery products facilities was causing problems with Hormel Foods' product flow. Product mix and number of supply items had grown creating an imbalance in storage locations for the inventory. Inputing data from a sampling of time, they used ExtendSim to model the different systems that were supplying and demanding material from bay locations at various rates, quantities, and shifts of operation. Hormel was able to determine the best alternative solution while verifying adequate inventory turns, minimizing equipment and material handling costs, and meeting capacity requirements.
An international manufacturer of heavy duty mining equipment built a custom library of blocks in ExtendSim. Each block represented a different piece of their rock crushing equipment. Their sales team was able to bring this tool to a customer site and build a model of the customer's entire crushing and screening process on the spot. They were quickly and easily able to create a technically and economically optimized solution for each customer's actual combination of feed material and operating conditions.
The complexity of truck loading was approached with the support of a simulation model by a beverage distribution company. Among the variables comprised to achieve shorter cycle time were the modification of the truck schedules and the amount of docks needed for each vehicle category.
For one of the pioneers in 3rd-party agrarian services, ExtendSim was used to approach the operation of temporary grain storage in “silo bags” during the crop harvest. Simulation was used to assess the requirements of process design, equipment, and investment decisions. Plus, it helped the agrarian service experts explore options of operative modes to optimize the deployment of resources in this critical instance during the harvest.
For a company focused in beverage distribution, simulation was used to calculate the size and profile of a fleet of trucks to serve retailers and supermarkets in the different areas of the Federal District. Among the more important requirements to be considered were: the capacity of the trucks, the maximum number of contacts in a route, the daily activity level - measured by the number of clients and the quantity requested by each client, and legal restrictions as the loading and unloading schedule allowed by the city. Simulation allowed them to find the optimal quantity of trucks to own, the quantity of hired trips, and the bundles transported by them (since it was paid by bundle and not for hired trip), and the prospective utilization level of the fleet.
ConAgra Foods reached out to the University of Idaho asking them to partner with them on a process improvement project. Since ConAgra is a heavy ExtendSim shop, they requested student teams use ExtendSim. Students were asked to evaluate the cost and effectiveness of in process inspection vs. end of process inspection in systems where the variation is often due to product mix, mean time to down times, and duration of down times instead of variation within the actual processing time.
- Major beverage retailer simulates product demand to optimize staffing levels at retail locations worldwide.
- Procter & Gamble uses ExtendSim to model everything from soup to nuts.
Case Studies

Ameen Menessi, Amr Hossam, Jana Amr, Seif El Yassin, and Shady Ayman
Arab Academy for Science, Technology and Maritime Transport
August 2025
The report presents a comprehensive study on implementing Digital Kaizen at a gum and candy manufacturing facility in Egypt, operated by Company X. The initiative aimed to reduce waste, enhance packaging line efficiency, and enable real-time quality monitoring by integrating traditional lean tools—like Fishbone diagrams and Pareto analysis—with digital technologies such as Power BI dashboards and dynamic sampling systems. A key component of the project was the use of ExtendSim to simulate the packaging line under both old and expanded capacities, incorporating real-world parameters like machine rates, MTBF, MTTR, and rework levels.
Simulation results demonstrated significant improvements with the expanded configuration: output increased by 31.8%, cycle times dropped by 10.3% on Line 1 and 50.6% on Line 2, and the rework rate decreased by 4.7%. These findings validated the effectiveness of the capacity expansion and highlighted the value of simulation modeling in supporting data-driven decision-making and continuous improvement, aligning with the principles of Digital Kaizen.
1Point2
Seyssinet, France
A major pharmaceutical company uses ExtendSim to simulate its packaging lines and optimize new line design. The company has gleaned a 30% time reduction in defining new line setup and regulation process since using simulation plus a 95% efficiency rate in their packaging lines.
Use of Simulation Models to Study the Dynamics of Perishable Produce Recall due to Non-Conformity through the Supply Chain
Patrizia Busato and Remigio Berruto, DEIAFA – University of Turin
3rd International European Forum on System Dynamics and Innovation in Food Networks
February 16-20, 2009
When a non-conformity occurs, the time to recall the produce depends on many factors: lot size, lead time for information spreading from link to link, product transit time among links, product storage procedures and times, and the point in the supply chain where the problem occurred. Using ExtendSim, the authors built a model to study different scenarios for a recall procedure.traceability process, often small size lots are merged together to form a large size lot at some point in the supply chain. This larger lot size could imply higher risk for the consumers in case of recall of the produce and much higher recall time and cost for the supply chain.Due to requirements of produce storage, the processing plant, and saving in the The supply chain for fresh produce consists of many links: producer/grower, warehouse, packing center, distribution center, retailers, and finally the consumer. Each of these is a system in itself, interacting with the other components of the supply chain.
Sherine Beshara, Khaled S. El-Kilany, Noha M. Galal
International Journal of Mechanical, Aerospace, Industrial, Mechatronic and Manufacturing Engineering Vol:6, No:5, 2012
World Academy of Science, Engineering and Technology
Perishability is a huge challenge on the performance of any Agri-food Supply Chain (ASC). The difference between ASC and any other supply chain is the effect of factors like food quality, food safety, and weather related variability. The ASC of fresh products, which are highly perishable, face problems of short product lifetime making it even more complex. This paper focuses on a two echelon agri-food supply chain: production and distribution. The production echelon is located in Egypt while the distribution echelon is in Holland. Using ExtendSim helped to evaluate and analyze the performance of these supply chains improving overall system performance.
Kevin T. Higgins
Food Engineering Magazine
August 2001
Packages that accurately emulate the hybrid processes that characterize food and beverage manufacturing are making simulation more than just a snazzy presentation tool for upper management. Virtual Engineering's New Frontier describes users roughing out their production and packaging lines on screen to gain insight into the dynamics of their lines and where and why bottlenecks occur.
Flow architecture simulation: a powerful approach to buffer dimensioning in high-speed packaging lines
S.A.Ricardo Rodríguez & Rosana Marino
S&T - Servicio y Tecnología
Pilot experience in the adoption of performance simulation approach to design, redesign, and acquisition of bottling lines for the Zarate plant of Cervecería y Maltería Quilmes S.A. This paper discusses the management of the huge bottling resources of the company: more than 36 lines in 12 factories, in 6 countries, with an aggregated investment value of $ 200 million, occupying more than a thousand people and producing 250 million cases a year of 300 different SKUs.
É. Hajnal and G. Kollár, Corvinus University of Budapest; G. Almásy, University of Veszprém; K. Kollár-Hunek, Budapest University of Technology and Economics
Applied Ecology and Environmental Research, vol 5, number 1
May 15, 2007
Any activity that receives inputs and convert them to outputs can be considered a process. So, essentially, similar equations are used in the theory of chemical, biochemical, nuclear, mechanical, and other types of process engineering modeling. This particular research group set out identify the processes, network of processes, process variables and process equations in food logistics. This paper introduces how process building, simulation run, and optimization can be carried out in a Food Distribution Centre with a message-based discrete event simulation software - ExtendSim. Simulation usage as a decision supporting tool in the hand of company management is introduced as well as the affect of wrong decisions on the extent of air pollution coming out from cooling vehicle.
Videos


Finite Plant Capacity Model
Gray McQuarrie, president of Grayrock & Associates, uses a discrete event model built in ExtendSim to look at issues of dealing with finite plant capacity. He also touches on design of experiments and neural networks.