Minimize computational requirements using the ExtendSim discrete rate approach for quicker and more efficient model execution.

Waste
Reduction
ExtendSim models examine the process plutonium and spent uranium fuel rods undergo as they are being turned into waste and/or mixed oxide fuels at the Savannah River Site.
The Tonkolili Iron Ore Project managed by African Mineral Limited uses a complete pit-to-port model inclusive of mine processing operations and stockpiling, single line rail network (for supply and export), port landside (car dumper, stockpiling, etc), and port marine (shiploading/unloading, inbound/outbound movement to anchorage etc).The model was calibrated to engineering and operational design specifications and real environmental conditions.

Pulp and
Paper Mills
A New Zealand pulp and paper mill models their integrated pulp mill, recycle facility, and sack kraft machine to determine the optimum mix of products and grades for specific economic conditions. Pulp and paper millThis mill now boasts bleached softwood kraft production costs in the bottom quartile worldwide.
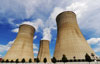
Fuel
Transfer
After the decommissioning of an experimental reactor at a national laboratory, ExtendSim was used to experiment with different nuclear fuel transfer strategies. The model identified which operational changes would play important roles in minimizing the required time to complete the rector refueling task. And, it gave management a better picture of system bottlenecks in need of removal in future operations.
ExtendSim for Process Flow Analysis
- Water and wastewater facility management.
- Evaluate possible combinations of shovels and trucks in order to achieve minimum production costs and reduce capital expenditures.
- Articulate sample theory.
- Test parameter changes to understand impacts before deployment and to reduce field trials.
- Help understand the different combination of mass and time.
- Examine the impact of making adjustments to settings.
Who is Using ExtendSim
DNV GL used ExtendSim for a concept selection study to optimize the system design and help convince shareholders of Borouge (an Abu Dhabi Polymers Company) that Borouge 2 would be a viable project that would be a good return on their investment. This new plant would be capable of producting two million tons of polyolefins. The model created was a rather complicated flow model with complex rules for running the plant in case of component failures. Though the time-frame was short, the model helped convince shareholders to move forward with the project.
In another project, DNV GL used ExtendSim to optimize the field development of an oil and gas site based on the analysis of possible component failures and flow assurance issues (e.g. hydrate formation, wax deposits and sand erosion) which might arise. Instead of this being a simple flow rate model, it was a complex thermo-hydraulic flow vector.
- An international manufacturer of heavy duty mining equipment built a custom library of blocks in ExtendSim. Each block represented a different piece of their rock crushing equipment.
Their sales team was able to bring this tool to a customer site and build a model of the customer's entire crushing and screening process on the spot. They were quickly and easily able to create a technically, and economically, optimized solution for each customer's actual combination of feed material and operating conditions.
- Optimizing the design and operation of a bio-refinery based on high-yield pulp, paper, and paperboard systems.
- Modeling sensor output from a nuclear fuel pyro-processing plant to assess alternative safeguard approaches.
- Duplicating the complete infrastructure of pulp and papermaking processes for training, testing, and optimization.
- An international metallurgical corporation uses ExtendSim to successfully maintain ISO compliance whilst optimizing sample sizes for health and safety requirements.
- Mining operations.
- Pulp and paper mills.
- Petrochemical industry.
- Pharma solutions.
Case Studies

Rob Brownie
Insight Acumen
2022
Check out this model of an Iron Ore Grade Movement Model where Insight Acumen was contracted late in the company model development process to support the decision maker, continue model development and incorporate required enhancements.
Major required enhancements were changes to business rules and routing for trains and information outputs for many key metrics.
For more customer and concept models, or more on Insight Acumen, visit www.insightacumen.com.au.
Rob Brownie
Insight Acumen
2020
Check out this case study for a coal handling and processing plant model built using ExtendSim. The intent was to be able to test operational strategies for run-of-mine. There were business rules for the three stockpiles and also for the stacker-reclaimer. Maintenance and weather impacts were modelled. Output priorities for product could also be changed, ie train or overland conveyor.
Major required enhancements were changes to business rules and routing for trains and information outputs for many key metrics.
For more customer and concept models, or more on Insight Acumen, visit www.insightacumen.com.au.
Rob Brownie
Insight Acumen
2020
Concept model for a deployable bulk fluid distribution system using ExtendSim. A good example of Item and Rate library blocks being used together. Simulates a Defence littoral area of operations, forward operating area. Fuel is delivered by tanker ships via 1.5km pipeline to large storage near coast. Large tanker trucks are filled from large storage and then deliver fuel to field bulk storage where F-34 aviation fuel is used for helicopter operations and F-54 diesel fuel is used for truck missions. Large storage near coast is resupplied by tanker ship when fuel level reaches a trigger level threshold.
For more customer and concept models, or more on Insight Acumen, visit www.insightacumen.com.au.
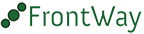
Energy Optimization in a Paper Mill Enabled by a Three-Site Energy Cooperation
Alexander Hedlund & Olof Björkqvist, Faculty of Science, Technology and Media, Campus Sundsvall, Mid Sweden University
Anders Nilsson & Per Engstrand, FrontWay AB, Norrkoping, Sweden
Although there are opportunities to reduce electrical energy demand in unit processes of mechanical pulp-based paper and paperboard production, this may not be financially beneficial. This is generally because energy optimization opportunities connected to reduced refiner electricity demand in mechanical pulping systems also results in less steam available for the drying of the paper. As modern high consistency refiner systems produce approximately one ton of steam for each MWh of electricity when producing one ton of pulp, a reduction in electric energy demand leads to increased fuel demand in steam boilers to compensate for the steam shortage. In this study, the authors investigated what the financial and environmental situation would look like if they were to expand the system border from a paper mill to a larger system consisting of a mechanical pulp-based paper or paperboard mill, a district heating system with an incineration boiler and a chemical pulp mill. Mechanical pulp production has a wood to product yield of >90%, a high electric energy demand to separate woodchips to pulp and is a net producer of heat and steam while chemical pulp-based production has a wood to product yield of 50%, a low electric energy demand and is a net heat and electricity producer due to the combustion of dissolved wood polymers. The aim of this research is to create useful and robust models of how to use excess heat from certain industry sites to cover the steam shortage in other industry sites by means of utilizing and optimizing the district heating systems connecting these sites. For this purpose, the authors used the FrontWay module with ExtendSim which dynamically allows them to evaluate different scenarios. Their results shows that there is great potential to reduce both carbon dioxide emissions and production costs for industry sites and society by means of these tools.
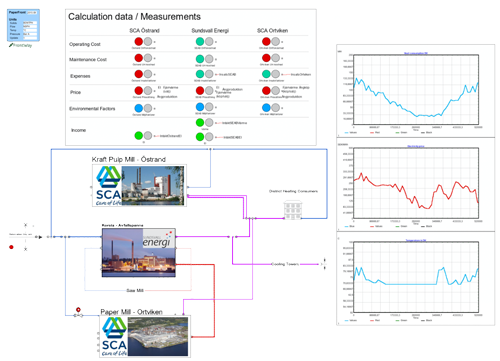
An Efficient Method for Optimal Design of Large-Scale Integrated Chemical Production Sites with Endogenous Uncertainty
Sebastian Terrazas-Morenoa, Ignacio E. Grossmanna, John M. Wassick, Scott J. Bury, Naoko Akiya Carnegie Mellon University • University of Melbourne, School of Chemistry
Computers & Chemical Engineering • Volume 37 • February 2012
Integrated sites are tightly interconnected networks of large-scale chemical processes. Given the large-scale network structure of these sites, disruptions in any of its nodes, or individual chemical processes, can propagate and disrupt the operation of the whole network. Random process failures that reduce or shut down production capacity are among the most common disruptions. The impact of such disruptive events can be mitigated by adding parallel units and/or intermediate storage. In this paper, the design of large-scale, integrated sites considering random process failures in addressed. In a previous work (Terrazas-Moreno et al., 2010), a novel mixed-integer linear programming (MILP) model was proposed to maximize the average production capacity of an integrated site while minimizing the required capital investment. The present work deals with the solution of large-scale problem instances for which a strategy is proposed that consists of two elements. On one hand, we use Benders decomposition to overcome the combinatorial complexity of the MILP model. On the other hand, we exploit discrete-rate simulation tools to obtain a relevant reduced sample of failure scenarios or states. We first illustrate this strategy in a small example. Next, we address an industrial case study where we use a detailed simulation model to assess the quality of the design obtained from the MILP model.
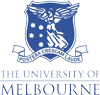
Polarimeter - Instrument Simulation
Richard Morrison
University of Melbourne, School of Chemistry
Simulations offer valuable insights into how an instrument can be expected to perform and can also point to areas for improvement. In the case of polarimeters described in this article, it is of interest to simulate the motion of the analysing polarizer relative to the fixed defining polarizer as this forms the basis for the optical rotation measurements. To make the simulation more realistic the author incorporated additional factors including (i) the broadband nature of the LED’s emission spectrum, (ii) the variation of the specific rotation of the sample as a function of wavelength, (iii) the spectral response of the detector and (iv) the temperature at which measurements are performed.
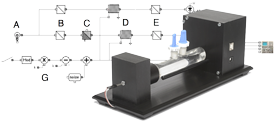
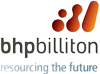
Simulating Time versus Mass Basis Sampling
M. Handyside and J. Ta'ala
Presented at Sampling 2014 Conference - The Australasian Institute of Mining and Metallurgy: Melbourne
July 29-30, 2014 in Perth, WA Australia
Mechanical sampling from conveyors has historically been a staple in the iron ore industry when information related to chemistry, sizing, and moisture is required. In order to optimize automatic sample stations in a changing production environment, BHP Billiton Iron Ore (BHPBIO) developed an ExtendSim model that enables the various combinations of mass–mass, mass– time, time–time and time–mass to be investigated. Their sample station model can utilize actual (variable) feed rates to achieve high resolution and enables the simulation of sample size variation. Cutter speeds and other settings can then be adjusted to better optimize the performance of the sample station with regards to optimal sample size. The model can also assist process engineers in adjusting settings to better optimize the sample station and reduce unwanted events such as blockages. The model can be easily modified to conform to various sample station designs. It is anticipated that the sample station model will be used by process engineers when looking at optimization and trouble shooting. The model is also being used as part of a training package to help new engineers understand the workings of a sample station and the impact minor adjustments to settings can have on sample mass and therefore compliance.
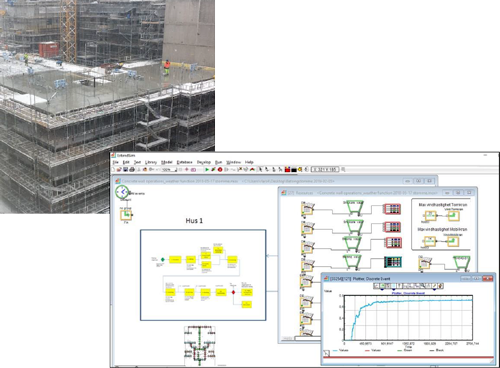
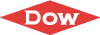
An Efficient Method for Optimal Design of Large-Scale Integrated Chemical Production Sites with Endogenous Uncertainty
Sebastian Terrazas-Moreno and Ignacio Grossmann of Carnegie Mellon University plus John Wassick, Scott Bury, and Naoko Akiya of Dow Chemical Company
This paper addresses the design of large-scale, integrated sites considering random process failures. Using a novel mixed-integer linear programming (MILP) model, the authors are able to maximize the average production capacity of an integrated site while minimizing the required capital investment. In this case study, ExtendSim is used to analyze a scenario reduction technique, reporting the results of simulating the operation of the Pareto-optimal designs.
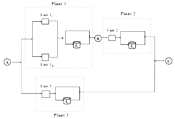

A Simulation-Enhanced Value Stream Mapping Approach for Optimisation of Complex Production Environments
David Schmidtke, U. Heiser, and O. Hinrichsen of the Technical University of Munich
Published in the International Journal of Production Research
May 16, 2014
Value stream mapping (VSM) is a widely adopted method for transformation of production environments into a lean operational state. However, attributes of the ‘paper and pencil’ approach result in limitations when applying VSM in complex production environments. Using ExtendSim, an enhanced VSM method is developed featuring a feasibility and trade-off analysis which is incorporated into the VSM procedure. A case study covering a process of exhaust gas purification catalyst production is then conducted to test the newly developed method. The VSM project yields a shop floor lead time reduction from 11.4 to 1.4 d.
Solution Providers

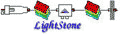
Analytical Chemistry
LightStone Software
Prof. Ed Voigtman, University of Massachusetts
Optical calculus solution to a wide variety of research and teaching problems.
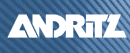
Chemical Process Control
IDEAS Simulation
Andritz AG
Process simulation software for the pulp & paper, oil sands, chemical, consumer products, and mining industry.
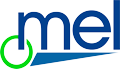
Chemical Process Control
THINK™ (Thermal Hydraulic Integrated Network)
Microfusion Engineering Laboratories (MEL)
Models that provide MEL clients with reliable simulators for their critical training requirements.
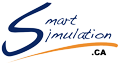
Mining
MineSimulator
SmartSimulation
To assist the decision making process in determining the number of productive resources (i.e. trucks, extraction equipment, and crushers) necessary to optimize mining operations and maximize production.
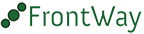
Pulp & Paper Making
PaperFront
Frontway AB
Library of blocks for ExtendSim describing the infrastructure of pulp and paper mills - pumps, chests and towers, mixing and splitting functions, and input/output of material.
Videos


SmartSimulation Value Proposition
(Video available in Spanish only) SmartSimulation has created a module of blocks in ExtendSim, MineSimulator, specifically designed to "Assist in maximizing production, optimizing the use of resources, and improving mine operations through a smart combination of Computer Simulation and Theory of Constraints principles."